Optimizing Your Welding WPS: Techniques for Improved Efficiency and Performance
Optimizing Your Welding WPS: Techniques for Improved Efficiency and Performance
Blog Article
Getting Welding Excellence: Revealing the Secrets of WPS Application and Optimization
In the realm of welding, accomplishing quality is a search that hinges on the thorough application and optimization of Welding Treatment Specs (WPS) By diving right into the crucial components, approaches, obstacles, and finest techniques associated with WPS, a world of welding excellence awaits those who are ready to discover its midsts.
Relevance of WPS in Welding
The Relevance of Welding Treatment Requirements (WPS) in the welding industry can not be overemphasized, offering as the backbone for ensuring consistency, top quality, and safety and security in welding procedures. A WPS gives comprehensive guidelines on how welding is to be performed, consisting of necessary variables such as materials, welding processes, joint design, filler metals, interpass and preheat temperature levels, welding currents, voltages, travel speeds, and a lot more. By sticking to a well-defined WPS, welders can preserve uniformity in their job, bring about constant weld high quality throughout various jobs.

Secret Components of WPS
Discussing the indispensable components of a welding procedure specification (WPS) is important for understanding its duty in welding procedures. One essential aspect of a WPS is the welding process requirements, which lays out the certain welding processes to be made use of, such as gas tungsten arc welding (GTAW) or shielded steel arc welding (SMAW) By integrating these key aspects right into the WPS, welding procedures can be standardized, ensuring quality, efficiency, and security in welding procedures.
Approaches for WPS Optimization

Secondly, training and certification of welding workers according to the details needs of the WPS is critical. Providing detailed training programs and guaranteeing that welders are certified to implement procedures detailed in the WPS can bring about better welds and minimized rework.
Additionally, leveraging innovation such as welding software program and monitoring systems can help in maximizing WPS. These tools can help in tracking variables, making certain parameters are within specified limitations, and giving real-time comments to welders, allowing them to make prompt changes for improved weld high quality.
Common Difficulties and Solutions
Facing challenges in executing the techniques for WPS optimization can prevent welding operations' performance and top quality. One usual challenge is insufficient training or understanding of the welding treatment requirements (WPS) amongst the welding team. This can cause inappropriate execution of welds, leading to defects and remodel. To resolve this, comprehensive training programs ought to be carried out to make certain that all welders are efficient in interpreting and using WPS precisely.
Another difficulty is the lack of appropriate documents and record-keeping, which is crucial for WPS optimization. Without clear documents of welding specifications, materials used, and examination outcomes, it becomes challenging to identify locations for renovation and make certain uniformity in welding processes. Executing a robust documents system, such as digital welding monitoring software program, can aid simplify record-keeping and facilitate information evaluation for continual improvement.
In addition, inconsistent welding equipment calibration and upkeep can position a substantial difficulty to WPS optimization. Routine tools checks, calibration, and maintenance timetables must be adhered to purely to guarantee that welding criteria are accurately regulated and preserved within the specified tolerances (welding WPS). By addressing these common obstacles with proactive remedies, welding procedures can boost effectiveness, high quality, and overall welding quality
Best Practices for WPS Execution
To guarantee effective WPS application in welding procedures, adherence to industry requirements and meticulous interest to detail are vital. When launching WPS execution, it is essential to start by extensively recognizing the specific welding needs of the job. This requires an extensive evaluation of the welding procedure specs, materials to be welded, and the environmental problems in which the welding will occur.
Once the requirements are clear, the next step is to select the suitable welding procedure that straightens with these requirements. This entails speaking with the relevant codes and criteria, such as those supplied by the American Welding Culture (AWS) or the International Organization for Standardization (ISO), to guarantee conformity and quality.
Additionally, documenting the whole WPS implementation procedure is important for traceability and top quality control. Comprehensive records ought to be kept regarding welding specifications, product preparation, preheat and interpass temperature levels, welding consumables made use of, and any deviations from the initial treatment. Regular audits and testimonials of click for more the WPS can browse around this site help determine areas for improvement and make certain recurring optimization of the welding process.
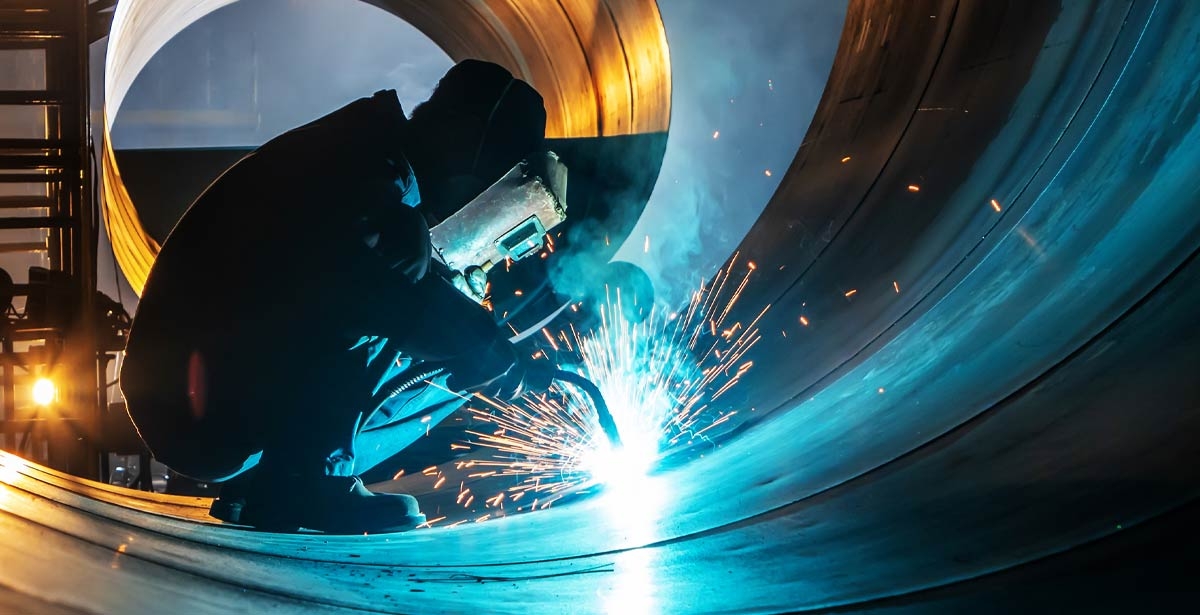

Conclusion
To conclude, the execution and optimization of Welding Treatment Specs (WPS) is crucial for attaining welding excellence. By recognizing the essential components of WPS, applying efficient methods for optimization, attending to common obstacles, and adhering to best methods, welders can make sure high-grade welds and risk-free working problems. It is vital for professionals in the welding industry to focus on the proper application of WPS to enhance overall welding performance and attain preferred outcomes.
The Significance of Welding Treatment Specifications (WPS) in the welding sector can not be overstated, offering as the backbone for guaranteeing uniformity, top quality, and security in welding procedures. A WPS offers detailed instructions on just how welding is to be carried out, including crucial variables such as materials, welding procedures, joint layout, filler steels, preheat and interpass temperature levels, welding currents, voltages, traveling speeds, and much more. One vital facet of a WPS is the welding procedure requirements, which outlines the specific welding procedures to be made use of, such as gas tungsten arc welding (GTAW) or protected metal official source arc welding (SMAW) By integrating these essential components right into the WPS, welding procedures can be standard, making sure quality, effectiveness, and safety in welding procedures.
It is vital for specialists in the welding sector to prioritize the appropriate implementation of WPS to improve total welding performance and attain preferred outcomes.
Report this page